What is Quality Control in Construction?
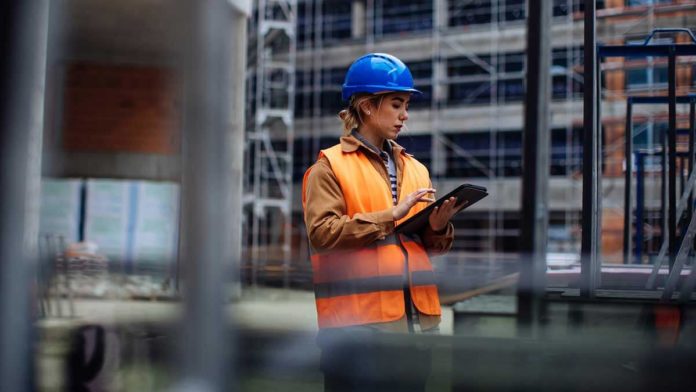
In the construction industry, quality control is not just about the client’s deliverables meeting the guidelines and standards set at the onset of the project. It also means maintaining effective safety measures for the job site.
In short, it can mean the difference between a project fraught with accidents and injuries and one that is accident and injury-free.
On the client side, many factors can be incorporated into a quality control system. It can involve testing completed services and goods to ensure quality assurance compliance, project completion within the scope of work, and ensuring compliance with regulatory bodies.
Quality control safeguards the project’s procedures and plans to achieve high-quality outcomes. This includes the client side as well as the company side. In order to provide high-quality deliverables to the client, the company producing the deliverables must have exceptional quality control standards as well.
Job site safety measures
A safe job site is a productive job site. Every project should have consistent standard safety measures in place with every project.
This can include perimeter security, equipment inspections and maintenance, PPE at all times, and a reporting protocol if there is a problem.
There may be other safety measures in place that are specific to the contract or type of project.
Compliance with federal and state regulations should also be a priority. OSHA has strict guidelines for work zone safety and failure to comply can result in significant fines and other penalties.
Adhering to quality control procedures can prevent accidents and injuries for workers as well as pedestrians, visitors, and others on or around the job site. A good portion of this protocol should be part of your standard operating procedures for any job under any contract.
Quality Assurance VS Quality Control
There are two basic parts to quality management: quality assurance and quality control.
Quality assurance in construction focuses on the fulfillment of the quality requirements by regulations, contracts, or company policy. It provides the definition and scope of “quality” as it relates to the contract or project.
Quality control is often confused with quality assurance, but the two terms do not mean the same thing. The correct definition of quality control concerns how well the quality assurance standards were fulfilled. It involves inspection and evaluation of the actual product or service.
The two terms go hand in hand but where quality assurance defines quality for the project, quality control ensures that the deliverable meets the standards set forth by that QA definition.
Benefits of having a QC process
Quality control is essential for customer satisfaction. Having that standard in place means your deliverables will consistently meet the contract requirements.
It also ensures fewer resources are wasted, thereby increasing efficiency and profits for the company.
The benefits of having a quality control process include:
- Increased customer satisfaction
- Increased sales
- Reduced production costs
- More effective use of resources
- Greater efficiency in production methods
- Increased employee morale
- Boost brand image and reputation
- Increased quality awareness
- Improved work site safety
- Fewer work site accidents and injuries
A construction quality control checklist that can be modified for the specific needs and requirements of each customer is a best practice measure that will help your company thrive and fully realize these benefits.
4 Objectives of Quality Control
While the primary purpose of a quality management system is to ensure the quality of the deliverables, there are four quality control objectives that support that goal.
- Reduce risks – Quality control reduces the risk of failure of the product or service, but it also reduces the risk on the work site.
- Increase product quality – Product failure can be very costly. In the construction industry, it can decimate a company. Quality control ensures a higher quality delivery as well as a safer one.
- Increase production efficiencies – A robust quality control system can significantly impact on every part of production. It touches every step from a safe and efficient work zone to a high-quality finished product.
- Encourage customer loyalty – When a company can consistently produce a high-quality deliverable that complies with the customer’s requirements, it builds a relationship between the company and the customer. When that customer needs a company they can count on to deliver what they need, they will choose the one with a proven track record, the one they trust.
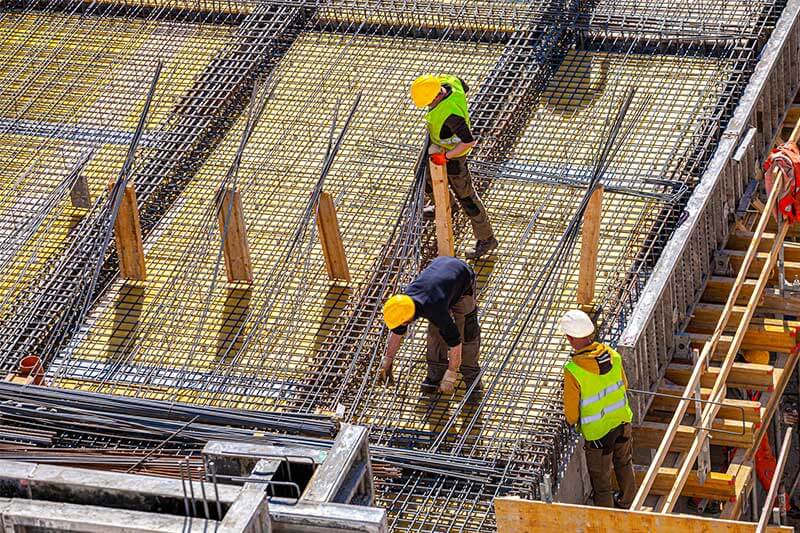
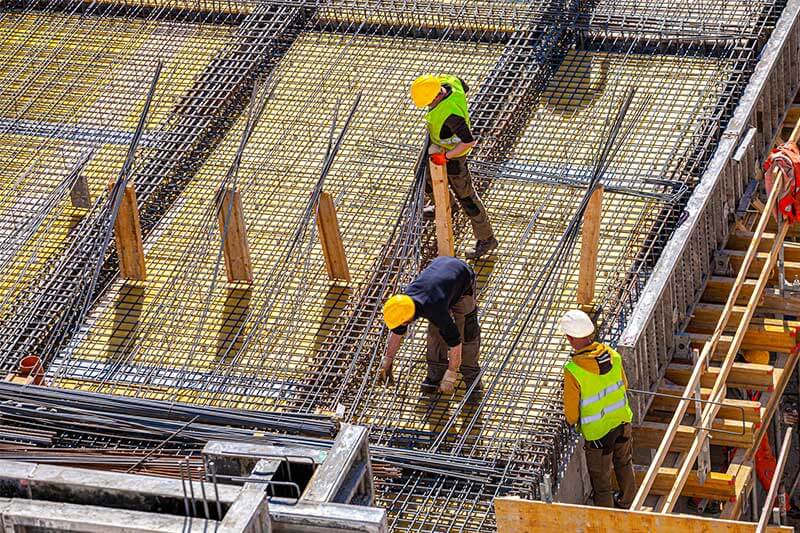
How to create a QC plan
While certain quality control measures are consistent for every job, each job should have its own plan to meet that customer’s specific requirements and needs.
Standard parts of a quality control plan include:
- Project Overview: Background, scope, deliverables, timeline, important deadlines and benchmarks
- Activities
- Organizational chart of leadership, staff, and external vendors
- Each worker’s title, qualifications, and responsibilities as it relates to fulfilling the requirements of the contract
- Who checks the quality of the project or work group
- Standards for suppliers, materials, and equipment
- List of suppliers who meet the standards
- Parameters for testing or evaluating the deliverables
- Clearly defined performance standards
- Documentation and evaluation of performance standards
- Criteria for acceptance of deliverables
- Quality control procedures specific to the contract
- Training
- Corrective actions
- Communication to include POC, communication protocols, etc.
- Safety and security measures for the job site, including securing the perimeter, equipment maintenance, etc.
For more tips on creating a construction planning guide, check out our in-depth guide!
How to Ensure Construction Quality Control
Ensuring quality construction starts before the project even begins. While it can vary a little from one company to the next, certain aspects are the same across the board. When implementing quality control protocols, construction professionals need to consider several things.
Establish clearly defined acceptance criteria as well as expectations. This makes sure that everyone is on the same page and has a clear understanding of what the client expects.
In addition to client specifications, this should include compliance with local, state, and federal laws and relevant regulatory codes.
Regular inspections of the project’s components and the job site should be a priority. At the project’s beginning, you should establish concrete information from the customer about what should be inspected at what point in the project timeline and what constitutes an acceptable result.
A quality control checklist can simplify inspections and prevent critical areas from being overlooked. A checklist also clearly communicates the areas where there are concerns or queries as well as the responsibilities of each worker.
Develop a protocol for correcting deficiencies and inaccuracies. This is the crux of quality control. In construction, this is critical. A defective product can be extremely costly and could affect lives.
Making a plan that allows for the time and equipment to address any areas that require correction is essential to the success of the project.
There should be an ongoing review and monitoring of progress, the work site, and the deliverables. This means regular inspections that allow you to address problems quickly and efficiently.
Construction safety standards
Construction safety standards should be implemented by your company as well as those by regulatory agencies like OSHA. Construction workers are at a greater risk of falling, getting pinned by heavy equipment, and inhaling toxic substances like silica dust.
Even pedestrians and those who are not on the job can be affected. If the job site perimeter is not secured, anyone can walk onto the site and can be injured or even killed. Without safety standards in place, everyone in the area is at risk.
A construction project plan can help minimize risks while streamlining portions of a construction project. For instance, if a fence around the perimeter is part of the plan, there will be clearly defined requirements for it, such as the type of fence, specified bases, how the fence is secured, and how many points of entry there are.
There are several areas of construction site safety that should be addressed.
Fall protection
OSHA has set forth specific regulations for fall protection for construction workers. This includes safety gear like harnesses and ensuring that on-site walking surfaces can support the workers who must walk on them.
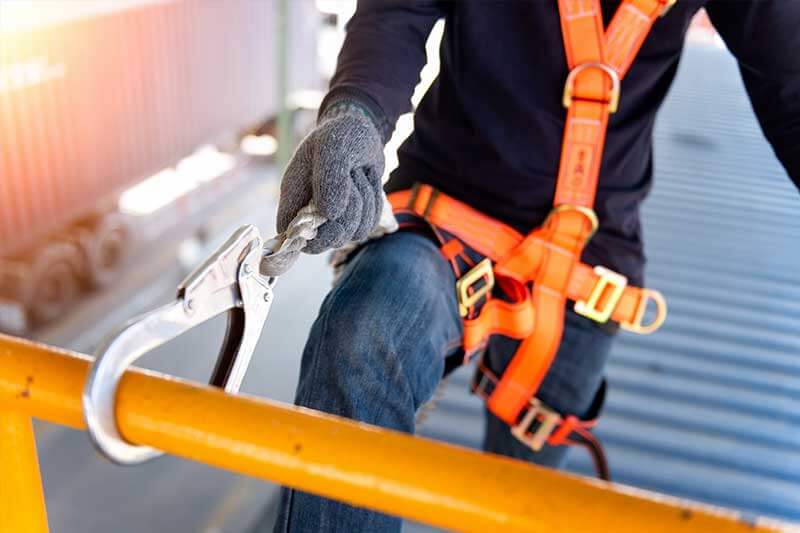
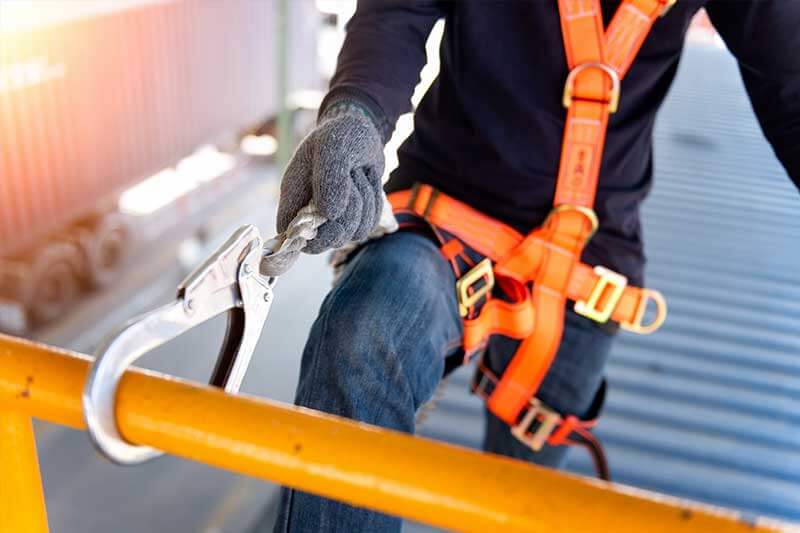
Fire protection
Fire protection OSHA regulations for construction workers protect them from various types of fire that can occur on a job site. It outlines requirements for fire safety gear and fire extinguishers to be available on the site.
General requirements
Construction workers have a right to a safe work area according to OSHA. There are several regulations in place that construction companies must comply with. They are designed to minimize injury and death on the job site.
Perimeter security
Perimeter security is a significant concern on a construction site because it does more than just keep the workers safe, it keeps the public safe as well.
However, a fence around the work site is not enough. It must be secured so that it does not fall over. A fallen fence can injure workers or pedestrians, cause accidents and damage property. These issues can be avoided by properly anchoring the fence with anchor bases.
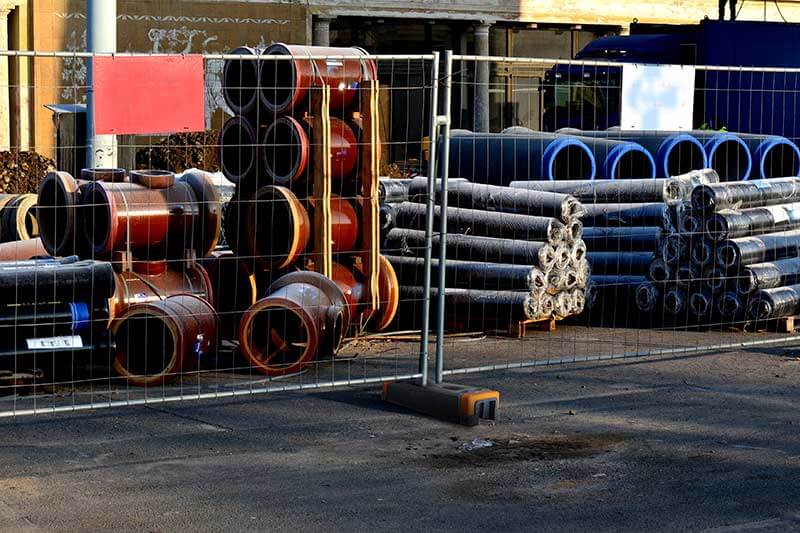
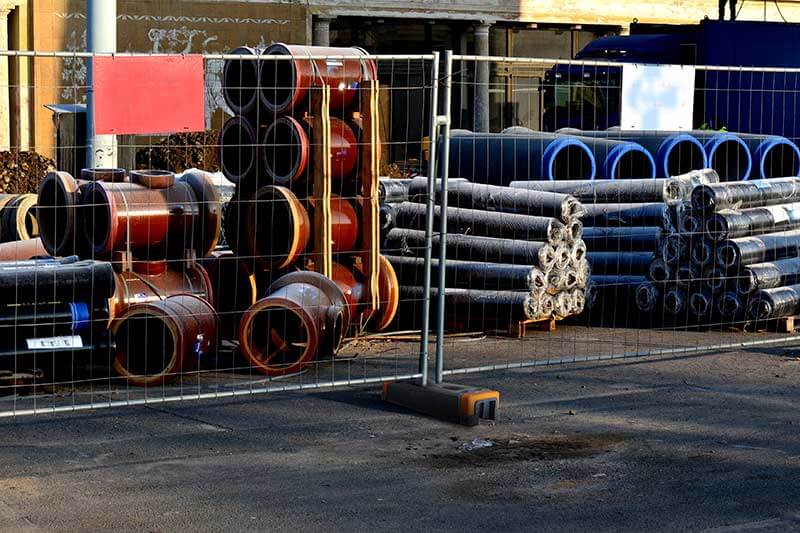
An anchor base is more durable and effective than concrete blocks, sandbags, or metal tube stands. You can choose from various types of anchor bases to find the one that best suits your fence, environment, and stability needs.
Trend now
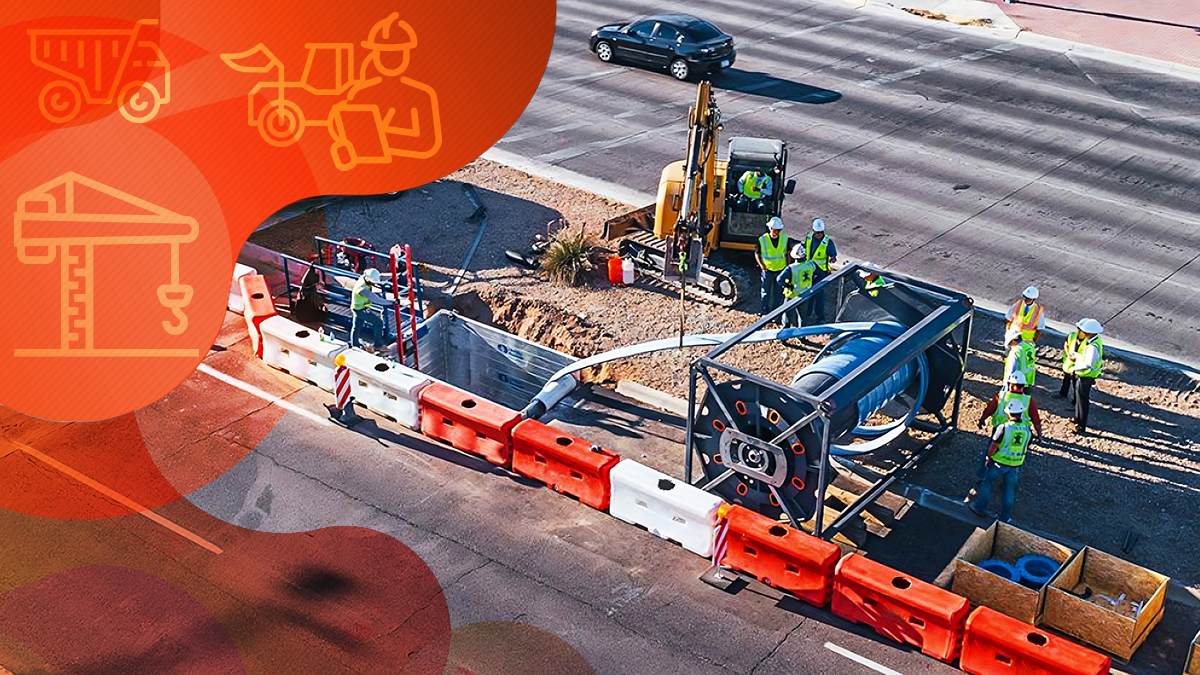
Reducing Impact Damage with Water-Filled Plastic Jersey Barriers
Understanding the effects of barrier materials on vehicles and their occupants can help improve road safety.
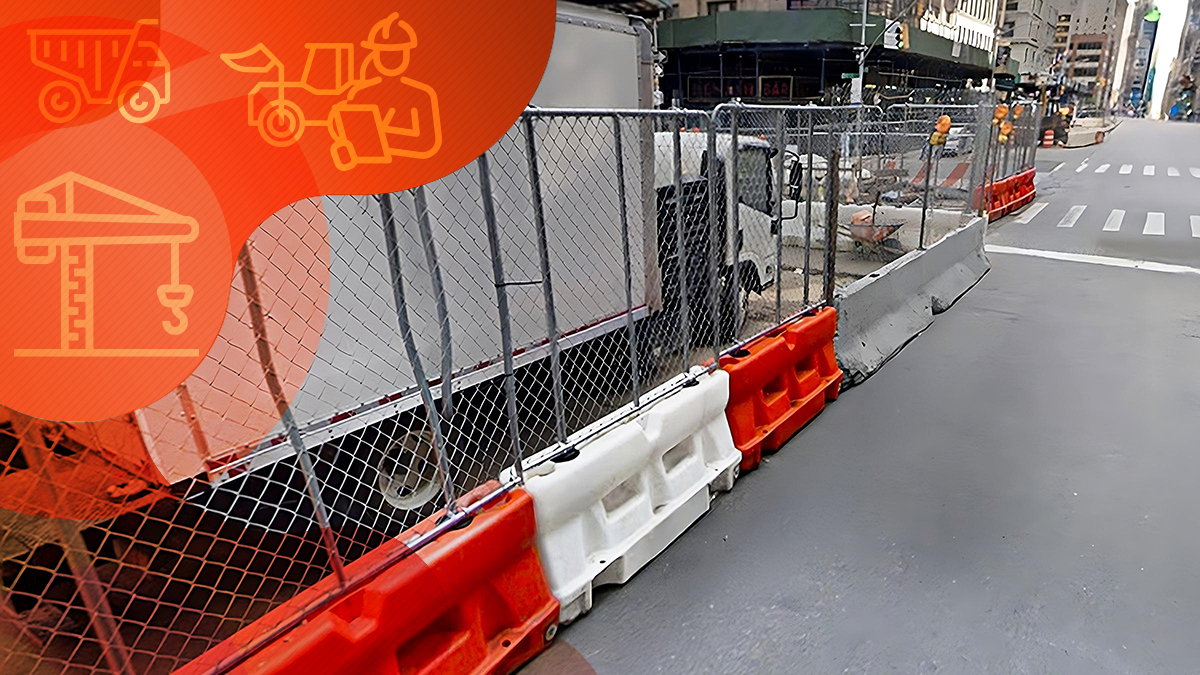
Choosing Between Concrete or Plastic Jersey Barriers
Not all barriers are built the same. Here’s what to know before choosing between plastic and concrete.
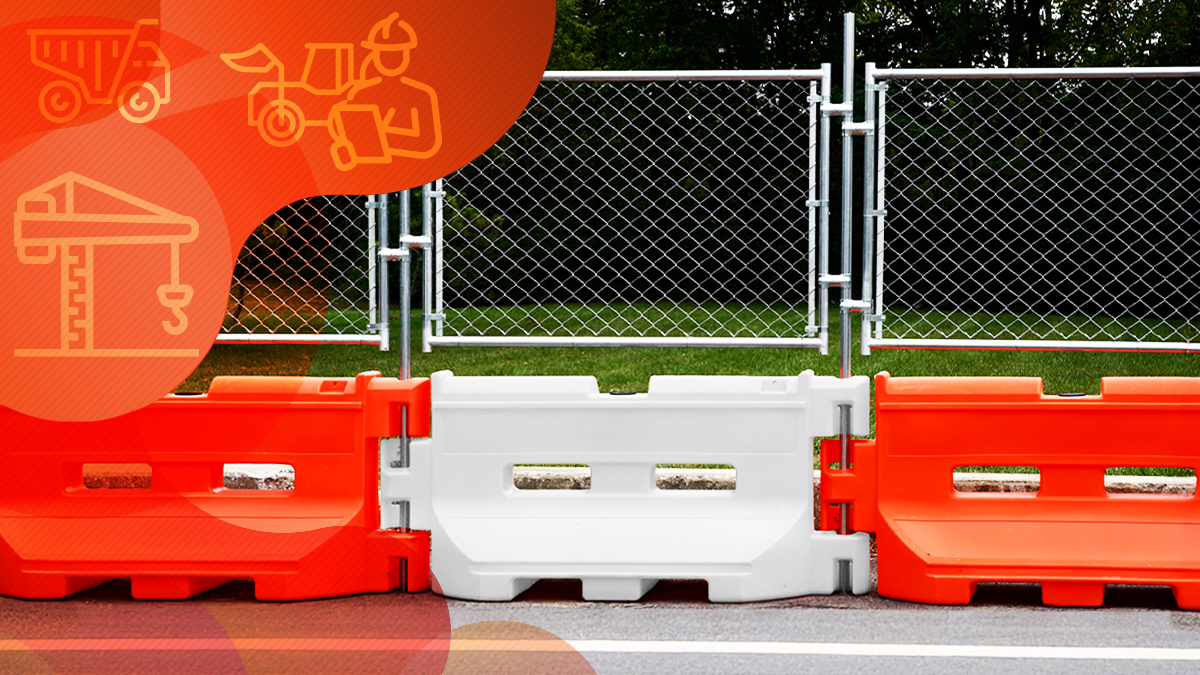
Advantages of Water Barriers with Fence Toppers
Learn how a fence topper transforms water barriers into a more secure, private, and effective work site solution.