What is a RFI in Construction
RFIs are a key part of the construction process, helping to maintain clear communication and avoid costly errors. Learn when and why they’re used.
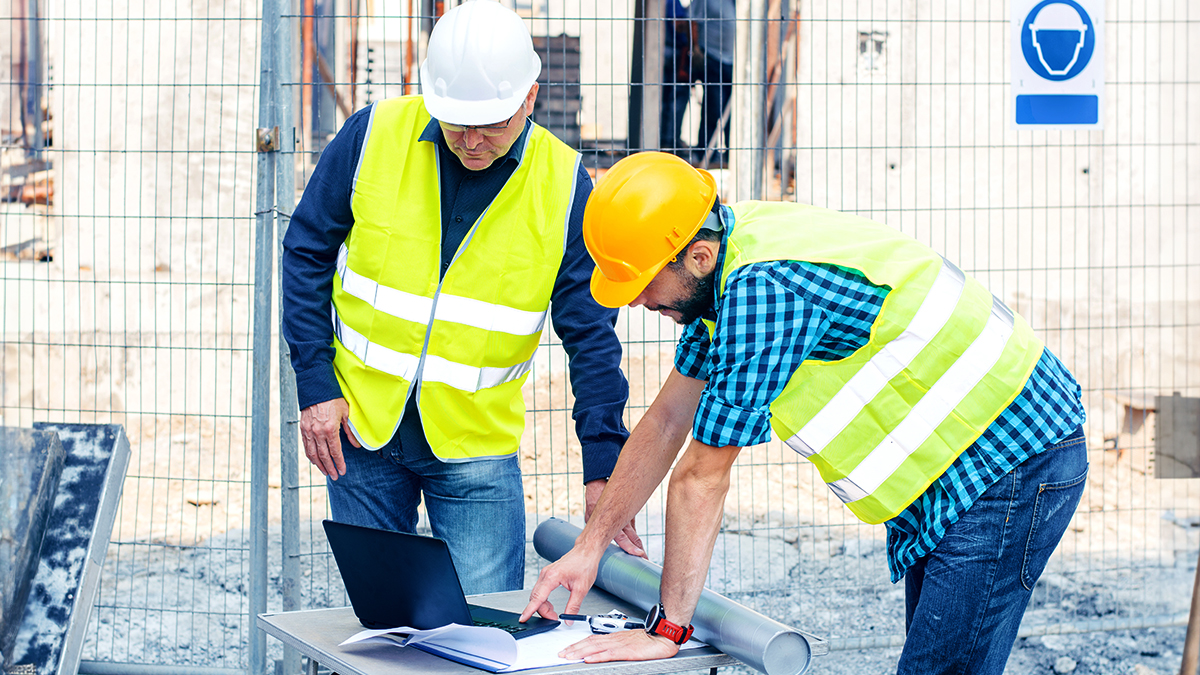
A request for information (RFI) is one of the "RFXs" in construction. Contractors may respond to a Request for Proposal (RFP) or a Request for Quotation or Qualifications (RFQ) as part of the bidding process.
They may receive a RFI before a contract is awarded or issue one during construction. Each request type serves a specific purpose during the procurement and building process.
How Does the RFP Process Work?
A RFP is a procurement document that describes a project and asks for bids from qualified contractors. Government agencies and large corporations use the process to identify a pool of contractors with the resources to complete the project. As part of the bidding process, stakeholders may issue RFIs or RFQs.
RFIs
RFIs may be used before, during, or after a RFP is issued. When they are used before a RFP release, they gather information about potential suppliers. The RFIs may ask questions about a company's experience, often focusing on specific requirements of the proposed project. For example, they may ask questions such as the following:
- Does your company have experience building on a floodplain?
- How many licensed heavy equipment operators does your company have?
- How many multi-year construction contracts has your company completed?
- Does your company have a safety plan?
Companies may use input to prepare a RFP or to identify a pool of qualified suppliers to receive a RFP.
RFPs
A request for proposal (RFP) begins the procurement process. The RFP defines the project, its goals, and the organization overseeing the contract. It sets a deadline for all submissions and an award date. In most cases, the RFP lists the evaluation criteria and how the award will be managed. Depending on the contract scope and size, the RFP process can take months to complete.
Once a RFP is issued, any questions or clarifications must be submitted in writing. Some organizations will include a specific process in the RFP, while others rely on RFIs.
RFQs
The group issuing the RFP may use a RFQ to ask for a bidder's financial and safety records. They may ask for documentation on licensing and employee information. These RFQs are requests for qualifications.
Alternatively, RFQs can be requests for a quotation. Often referred to as "asking for pricing," RFQs may be issued to a subset of bidders at the end of a RFP review or used to solicit pricing for standardized goods or services.
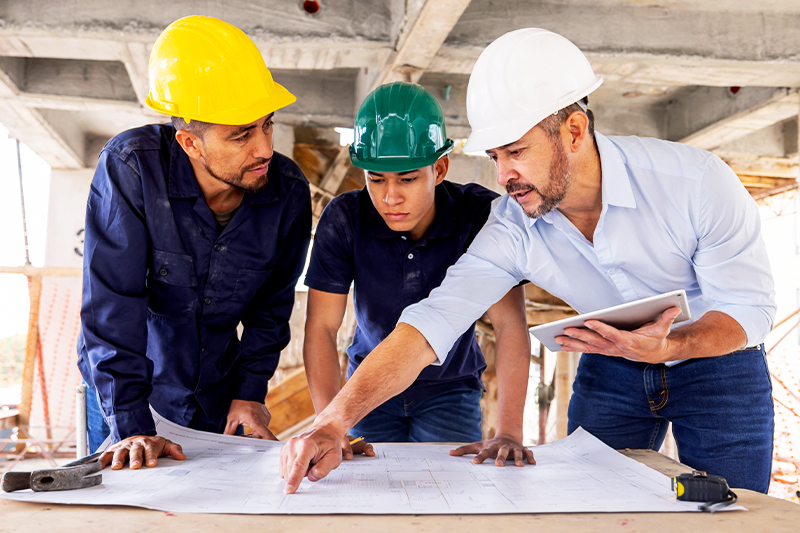
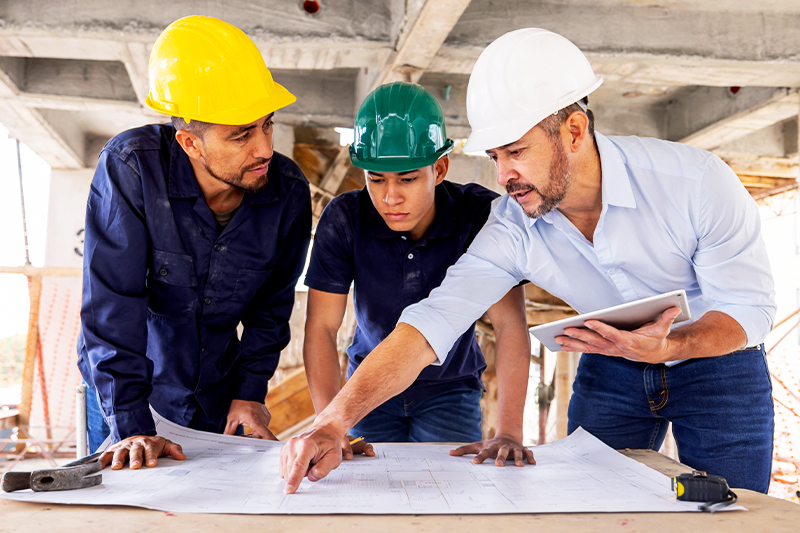
When to Use a RFI
Once a contract is in place, RFIs are used to request clarification on drawings, specifications, and project documents. They are designed to resolve ambiguities, capture specific decisions, and fill information gaps. Any stakeholder in the construction project can issue a RFI.
Over a dozen types of RFIs may be used during construction. Some of the most common are:
- Design Clarification. As work progresses, contractors may have questions about design drawings or specifications.
- Design Coordination. Stakeholders may issue RFIs to establish communication and organizational processes for a project.
- Constructibility Issues. Contractors submit RFIs when they consider site conditions, proposed materials, or design requirements to be unsafe or unfeasible.
- Scheduling. Contractors may need to change the schedule or adjust task sequences due to resource constraints, such as a lack of materials or labor.
- Incomplete Specifications. If errors or omissions are discovered, a RFI is used to determine how to fix the mistake or clarify the design.
- Change of Method. Contractors use RFIs to request a change in how a portion of the project is constructed.
- Deleted Scope. RFIs are used to alter a project's scope by deleting some tasks.
- Material Change. Material-related RFIs identify changes in materials due to delivery schedules, compliance concerns, or feasibility.
- Site Conditions. Unexpected or unsafe site conditions require a RFI to document the problem and suggest possible solutions. It may include the placement of new or existing utility lines.
- Value Engineering. Contractors may find cost-saving measures or suggest adjustments to increase the building's value. They submit RFIs to inform stakeholders and generate discussions on how to proceed.
RFIs are an accepted method of communicating changes to an original contract or plan to all stakeholders and asking for guidance or acceptance of the proposed changes. Understanding what should be in a RFI can help move projects forward with less rework and fewer errors.
What to Include in a Construction RFI?
RFI templates are available from multiple sources and may be included with construction project management software. Regardless of the source, a RFI should consist of the following:
- Project name, number, and address
- RFI number for tracking
- Unique RFI title
- Submittal date
- Response deadline
- Name, title, company, and contact information for initiating party
- Description of the request
- Name, title, company, and contact information for responding party
- List of attachments
- Potential cost of schedule changes
A standardized form or template can reduce the time it takes to prepare and respond to a RFI.
Best Practices for Using a RFI in Construction
RFIs should be used to effectively communicate and resolve the inevitable changes that come with any construction project. They should not be used to generate conflict over contract language or other factors that do not pertain to project completion. The best start to an effective RFI process is to have a procedure.
Have a RFI Process
RFI tracking ensures a transparent process that keeps all parties informed. Whether manual or electronic, every RFI should be assigned a sequential number. A tracking system should record where a RFI stands in the process. It may include the RFI question and reference the response.
RFI procedures may be incorporated in the contract terms. If not, they should be received before work begins. At a minimum, a RFI process should:
- Explain how to request a tracking number.
- Identify who is responsible for tracking a RFI.
- Stipulate the response times.
- List what qualifies as a RFI.
- Provide a RFI template.
- Establish what supporting documentation is required.
Each stakeholder should have an internal process for tracking RFIs to ensure timely responses.
Ask a Question
RFIs are often difficult to follow and hard to understand. They may lack crucial clarifying documentation. Unclear language contributes to confusion and misunderstanding. That's why a RFI should ask a question and only one question.
For example, a contractor needs to change the work schedule to accommodate material delivery delays. Changing materials can avoid the delay, so the contractor submits a RFI for approval.
The RFI request could be: "Can material x be used instead of material y?" The reason behind the request can be explained as part of the RFI description.
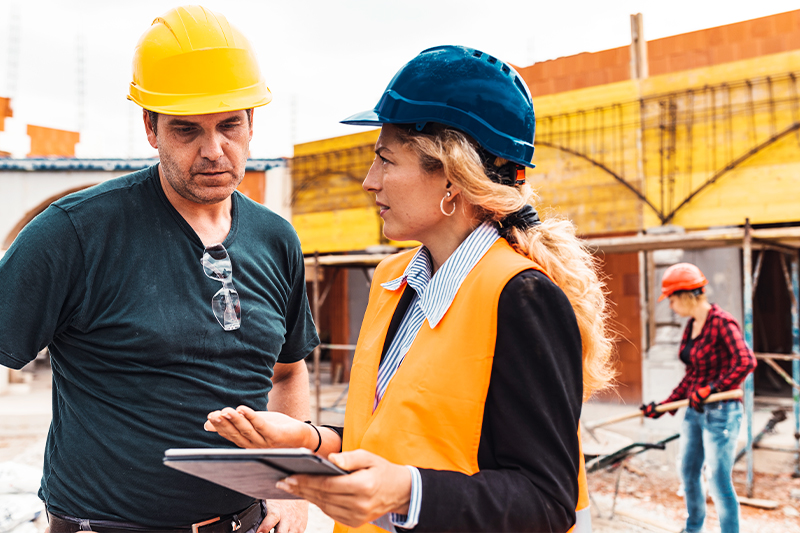
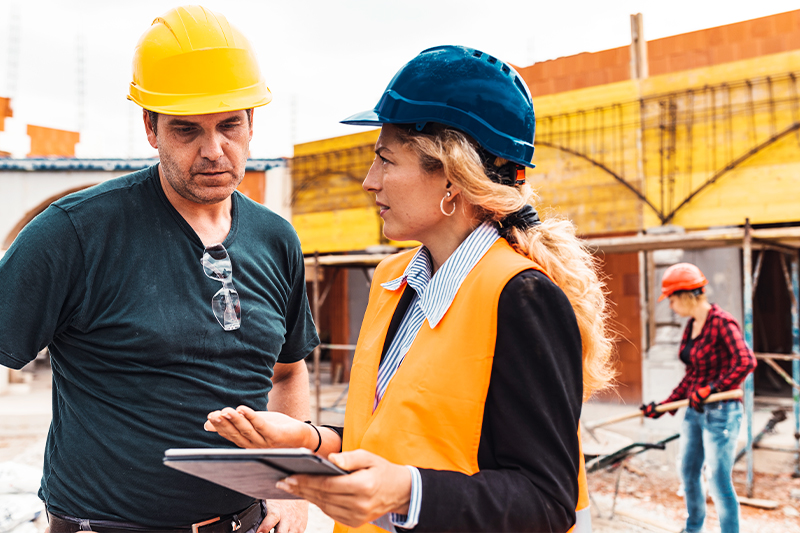
Provide Options
Whenever possible, present options as part of the request. If engineers only have to choose an answer, they are more likely to respond promptly.
Suppose a contractor has a problem with the location of existing water lines. The RFI could ask: "Is it possible to move the parking garage entrance 15 feet to the north to accommodate an existing water line?" The description can explain why the request is necessary and list the supporting documentation.
The engineers or architects can agree with the request or submit an alternative solution. Either way, the RFI moves the project forward, avoids delays, and ensures it remains within budget.
Respond Promptly
Although most RFIs flow from the contractors to the designers, there are times when an engineer or architect may have a question. When receiving a RFI, log it by number and question. Use an internal process to ensure a prompt response.
As part of the response, be sure to include the impact of each proposed option on project schedules and costs. For example, a request to relocate an interior wall should identify what is required to execute the change. If an alternative is available, the option should be included with the associated impact.
The RFI process aims to establish a clear communication channel to minimize errors and rework during a construction project. However, RFI misuse can cause friction and project delays. Proactively addressing RFI challenges in construction can result in successful working relationships.
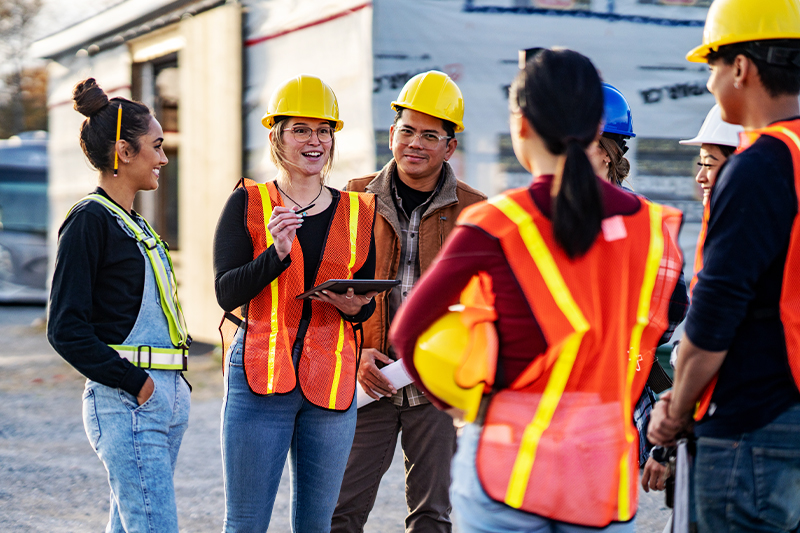
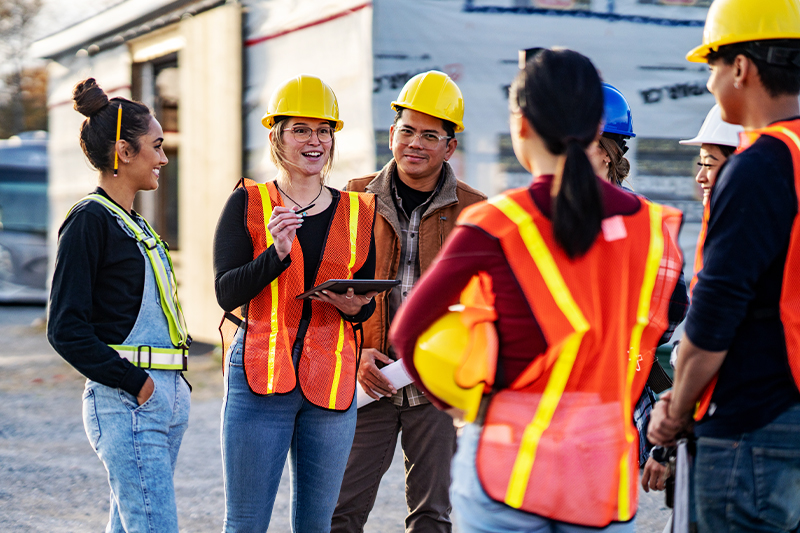
Challenges in RFI Construction
The RFI process, when used appropriately, keeps a project moving forward. However, the process can be abused. If stakeholders do not understand or lack training, unnecessary RFIs can be issued.
Know Your Contract
Before creating a RFI, stakeholders should review the contract and supporting documents. Simple language clarifications can be handled through other communication channels, reserving the RFI process for its intended use.
RFIs are time-consuming and expensive. A RFI cycle averages $1,080 from issuance to response and takes about ten days. Over 20% go unanswered. Having a documented process that stipulates when a RFI should be used can save everyone time and money.
Incorporating best practices into every RFI process can eliminate some of the ongoing challenges such as delayed response times and unclear or incomplete RFIs. It can reduce friction among stakeholders when unnecessary RFIs are issued.
Be Proactive During The Bidding Phase
Contractors should proactively address these challenges by understanding the construction bidding process.
During the bidding phase, contractors review bid documents such as plans, specifications, and terms. If any details are unclear or need further explanation, contractors can issue a RFI to the project owner or architect.
This helps to prevent misunderstandings and errors in the bid.
After the contract is awarded, RFIs continue to be a tool for addressing any new questions or issues that arise. This ongoing communication helps to maintain project alignment and promptly address any discrepancies.
Any changes or modifications to the original plans and specifications, often resulting from RFIs, are documented and approved by relevant stakeholders. This documentation is crucial for quality control, as it provides a clear record of agreed-upon adjustments and ensures that all changes are implemented correctly.
By being proactive and understanding all processes in the construction industry, third-party contractors can contribute to better outcomes and increase their chances of being awarded more contracts in the future.
To learn more about construction quality control, check out this detailed guide.
Trend now
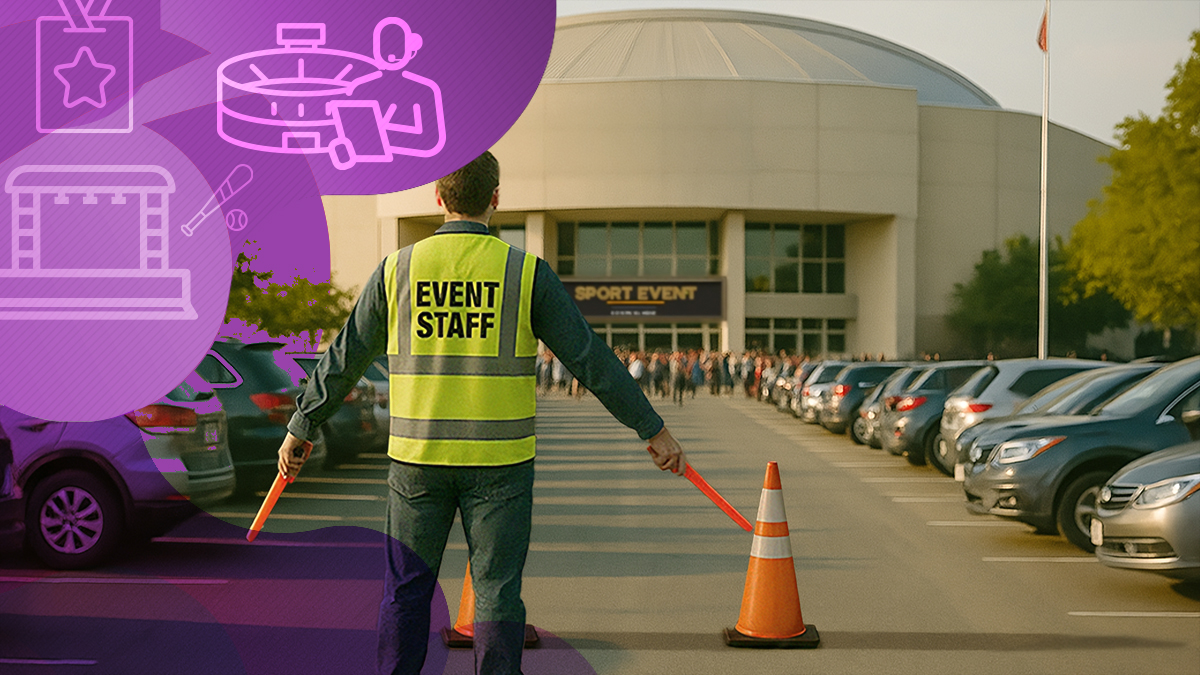
Parking Lot Safety Tips for Venues and Arenas
A safe and efficient parking lot sets the tone for the entire event experience, starting from the moment guests arrive.
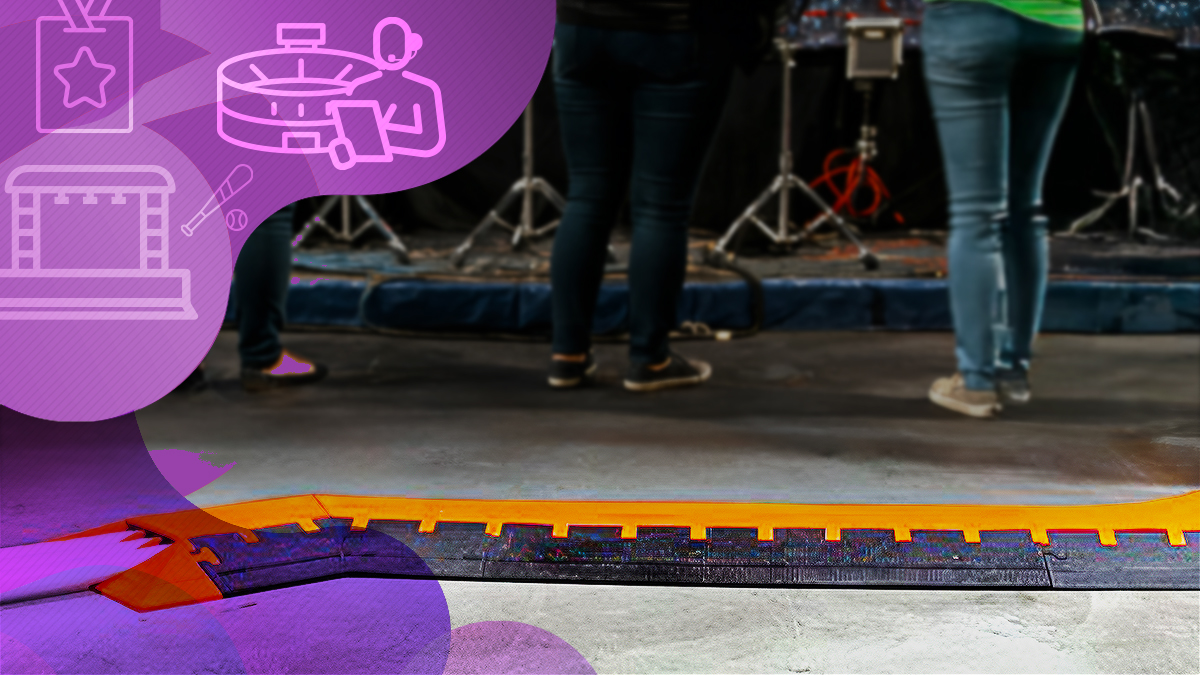
How to Choose Cable Protectors for Event Venues
Managing cables at large venues requires more than tape and luck. It calls for the right cabel protectors built for real-world conditions.
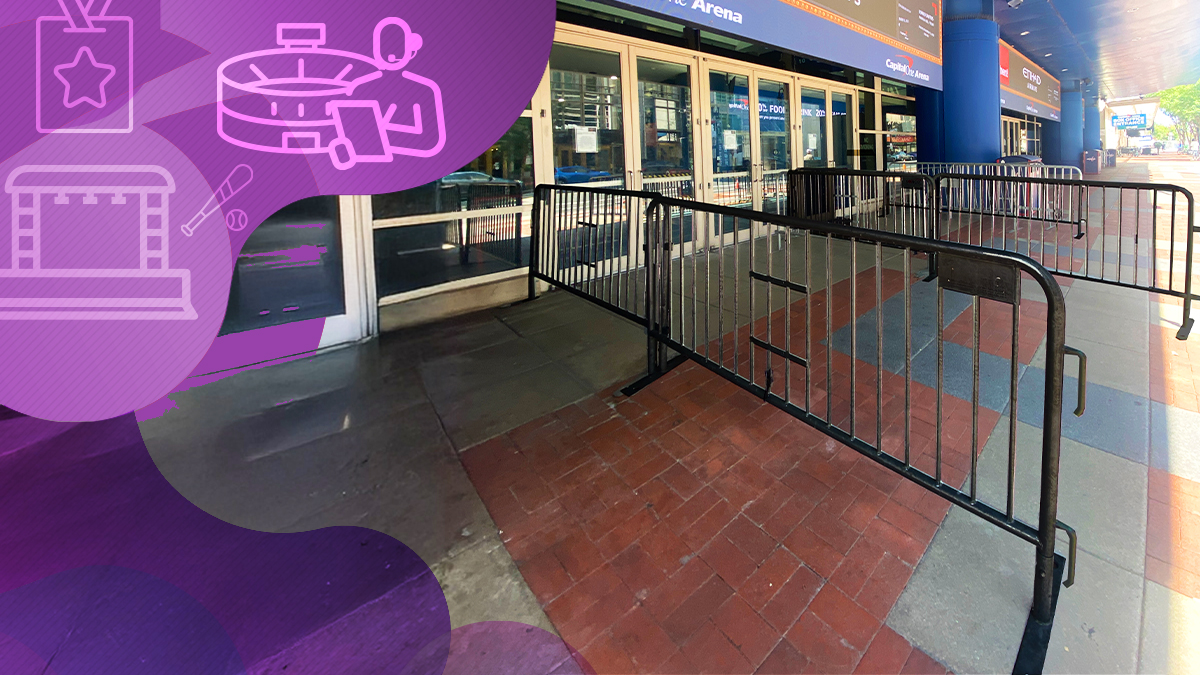
Best Crowd Control Barricades for Event Venues
If you’re planning events at scale, knowing what to expect from metal barricades can help you avoid common safety and setup pitfalls.